Sand Cooling Machine
The Sand Cooling Machine is specifically designed to cool return sand to the optimal temperature before it enters the sand mixer. Equipped with a feedback system for both inlet and outlet sand temperature and moisture, this machine ensures precise control and maintains ideal sand conditions for foundry operations.
Material:
- High-quality steel
Features:
- Stepless water pouring control supports a broader range of sand temperature and moisture levels.
- Prevents bridging caused by excessive water and reduces sticking of sand.
- Reliable and efficient operation to enhance productivity.
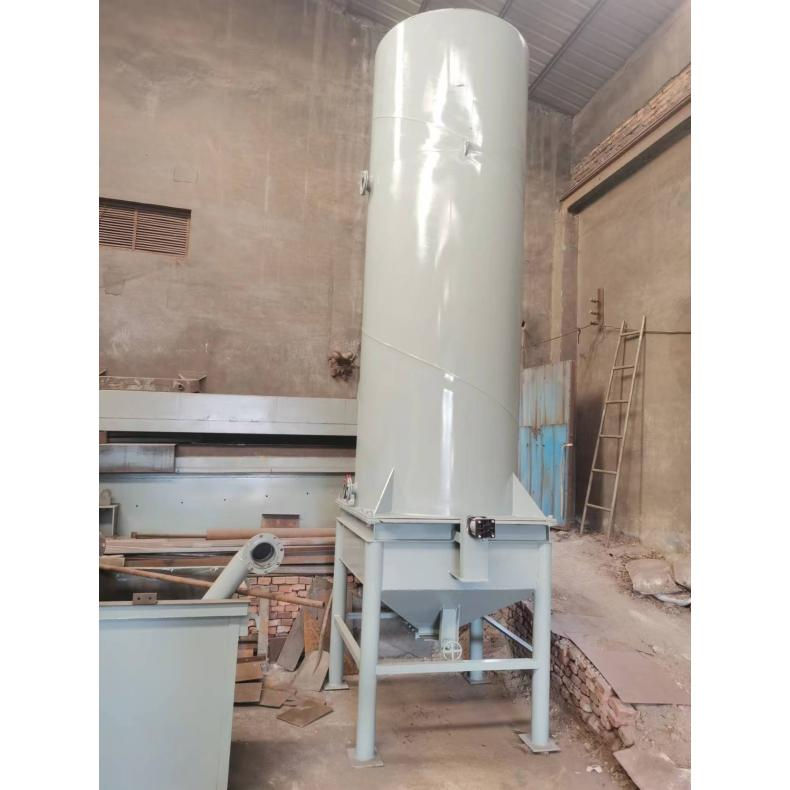
Sand Cooling Machine Specifications:
- Customizable to meet specific client requirements, with sizes and capacities tailored to individual cases.
- Standard options include capacities of 5t/h, 10t/h, 20t/h, 30t/h, and 60t/h.
Sand Cooling Machine is a dependable solution for maintaining consistent sand quality and improving overall casting process efficiency.
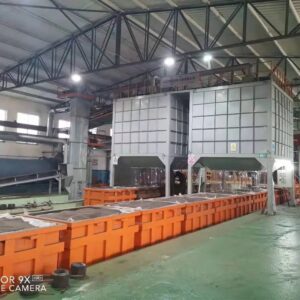
Key Procedural Steps in V-process Casting
- The lost foam casting (LFC) process is a precision casting method that uses expendable foam patterns to create complex metal parts. Below is a structured breakdown of the process based on your source material, along with key considerations and applications:
1. Pattern Material Selection
- Aluminum Die Castings:
Use expandable polystyrene (EPS) with pentane as a blowing agent.
Why: EPS is lightweight and decomposes cleanly at aluminum’s lower melting point (~660°C). - Cast Iron/Steel Parts:
Use a copolymer of EPS and EPMMA (expanded polymethyl methacrylate).
Why: The copolymer withstands higher temperatures (iron: ~1,200–1,500°C; steel: ~1,370–1,500°C) and reduces residue.
2. Pre-Expansion
- Process:
EPS beads are pre-expanded in a fluidized bed dryer using pentane (a volatile hydrocarbon).
Purpose: Increases bead size (typically 20–50x) to achieve target density (e.g., 20–30 kg/m³). - Key Control: Temperature and residence time to ensure uniform expansion.
3. Molding
- Tooling: Pre-expanded beads are blown into a metallic permanent mold using compressed air.
- Bonding: Heated (100–120°C) to fuse beads via steam, forming the foam pattern geometry.
- Pattern Design: Complex geometries are split into sections for easier molding, then assembled post-foaming.
4. Pattern Assembly & Gating
- Cluster Assembly:
Multiple foam patterns are mounted onto a gating system (typically EPS) to form a cluster.
Purpose: Enables simultaneous casting of multiple parts in one pour. - Gating Design: Channels must optimize molten metal flow and minimize turbulence.
5. Coating Application
- Refractory Coating:
Clusters are dipped in a water-based ceramic slurry (e.g., alumina, zirconia) to form a 2 mm coating.
Functions:- Prevents sand erosion during pouring.
- Creates a barrier to reduce gas defects from decomposing foam.
- Enhances surface finish.
- Drying: Coated clusters are dried thoroughly to avoid steam explosions during casting.
6. Mold Preparation
- Sand Compaction:
Coated clusters are placed in a flask, surrounded by unbonded quartz sand (grain size 0.1–0.4 mm).- Sand Raining Feeder: Ensures even distribution.
- Vibrating Table: Compacts sand to 90–95% density for stability.
- Sprue Exposure: Only the gating system’s sprue remains exposed for metal pouring.
7. Casting
- Pouring:
Molten metal is poured into the sprue. The heat decomposes the foam (EPS vaporizes; copolymer may leave minor ash).- Metal Flow: Fills the mold cavity precisely, replicating the foam pattern.
- Gas Management: Decomposition gases (pentane, styrene) vent through the permeable coating and sand.
- Critical Factors:
- Pouring temperature and speed to avoid turbulence.
- Foam degradation rate must match metal front advancement.
8. Demolding & Post-Processing
- Solidification: Metal cools in the sand mold (time depends on part size and alloy).
- Shakeout: Sand is removed via vibration, revealing the casting cluster.
- Cutting: Individual castings are separated from the gating system (e.g., sawing, grinding).
9. Sand Recycling
- Reclamation:
Used sand is cleaned (screening, thermal reclamation) to remove debris and residual coating.
Benefits:- Reduces material costs by 90–95%.
- Environmentally sustainable (minimal waste).
Key Advantages of Lost Foam Casting
- Complex Geometries: No cores or draft angles needed (e.g., engine blocks, pump housings).
- Dimensional Accuracy: ±0.3 mm tolerance achievable.
- Surface Finish: 3–6 μm Ra (reduces machining).
- Cost-Effective: Low tooling costs for prototypes/small batches.
Common Applications
- Automotive: Cylinder heads, intake manifolds.
- Industrial Valves/Pumps: Internal passages cast in one piece.
- Art/Decorative Castings: Intricate details preserved.
Challenges & Mitigation
Issue Solution Gas porosity Optimize coating permeability Incomplete filling Adjust foam density/pouring speed Sand collapse Improve compaction vibration settings
This process is ideal for industries prioritizing complex designs, reduced machining, and sustainability. Let me know if you need further details on specific steps!
- Aluminum Die Castings:
Features of V-process Casting
- High Casting Quality at Low Cost:
The process delivers excellent casting quality while maintaining cost-effectiveness. - Material Versatility:
There are no significant material limitations, allowing for a range of suitable sizes. - Precision and Surface Finish:
Achieves high precision and a smooth surface finish, reducing the need for extensive cleaning and saving on machining time. - Reduced Internal Defects:
Significantly minimizes internal defects, resulting in a compact casting structure. - Large-Scale Mass Production:
Capable of supporting large-scale and mass production of components. - Ideal for Repeated Castings:
Particularly suitable for the mass production of identical castings. - Flexible Operation:
Adaptable for both manual operation and automated production line control. - Environmental Compliance:
The production line’s operational status meets environmental protection technical parameters. - Improved Working Conditions:
Enhances the working environment and production conditions in the casting line, reducing labor intensity and energy consumption.
These features collectively position lost foam casting as a highly efficient and sustainable option in the manufacturing of complex castings.