Pouring Equipment for Casting
The pouring equipment for casting (Foundry Pouring Ladle for Molten Steel) is designed for efficient and safe pouring operations. After receiving liquid metal from the blast furnace, the ladle is transported to the molding site for precise pouring. It features a worm and gear mechanism that ensures smooth, flexible two-way rotation with excellent reversibility.
Available in manual and manual-electric dual operation modes, the ladle caters to diverse needs. The manual mode offers simplicity and ease, while the electric mode enhances safety and reduces labor intensity.
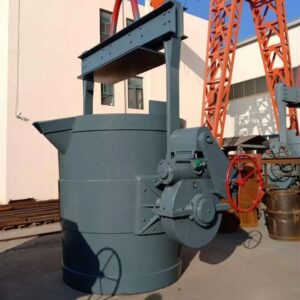
Features of Foundry Pouring Ladle for Molten Steel
- Optimal Rotation Center: The ladle’s rotation center is carefully designed for convenient operation, ensuring proper alignment and reducing effort when pouring is completed.
- Double Worm Gear Transmission: This advanced transmission system offers smooth and flexible operation with precise, reversible control, despite its high manufacturing requirements.
- Spray-Proof Design: Equipped with specialized spray-proof features to prevent molten metal from entering the gearbox, ensuring enhanced safety and durability.
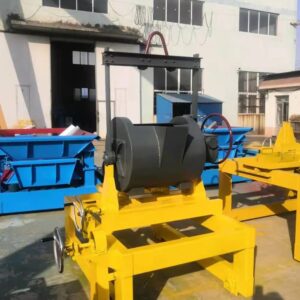
This robust and reliable equipment is an essential tool for foundry operations, designed to deliver efficiency and safety in molten steel pouring.
Capacity (T) | 0.3 | 0.5 | 0.75 | 1 | 1.5 | 2 | 2.5 | 3 | |
Barrel outline (mm) | Top diameter φ1( mm) |
520 | 606 | 643 | 722 | 830 | 897 | 943 | 1020 |
Bottom φ2 (mm) | 468 | 551 | 574 | 652 | 750 | 810 | 853 | 920 | |
Barrel height H (mm) | 540 | 590 | 665 | 740 | 860 | 910 | 960 | 1035 | |
Width A (mm) | 1070 | 1136 | 1207 | 1260 | 1380 | 1437 | 1550 | 1621 | |
Height B (mm) | 1310 | 1349 | 1456 | 1479 | 1856 | 1890 | 2057 | 2131 | |
Clearance height E (mm) | 45 | 50 | 55 | 60 | 70 | 80 | 85 | 90 | |
Patching thickness (mm) | Side wall b | 35 | 40 | 45 | 50 | 60 | 60 | 65 | 90 |
Ladle bottom b1 | 45 | 50 | 55 | 60 | 70 | 75 | 80 | 70 | |
Hand wheel radius R (mm) | 200 | 200 | 250 | 250 | 350 | 350 | 350 | 350 | |
Speed radio i | ≤70 | ≤100 | ≤180 |
Bottom Injection Type Ladle Overview
The Bottom Injection Type Ladle is designed for precision pouring and enhanced safety during foundry operations. It comes in two primary pouring types:
- Plug Rod Bottom Injection Type
- Sliding Nozzle Bottom Injection Type
Both types are available with hook-type or bearing-type gantries for flexible usage.
Key Features
- Plug Rod Bottom Injection Mechanism
- Equipped with a sliding rod clearance elimination mechanism to maintain alignment between the plug rod center and the nozzle center after repeated uses.
- Durable Construction
- The boom is forged, offering superior safety and reliability compared to steel weldments.
- Thicker steel plate for the ladle body and a reinforced bottom structure using a combination of taper, bottom hoop, and welding ribs enhance durability and operator safety.
- Hinged Pallet Design
- The ladle body and boom are equipped with hinged pallets that can be locked securely at any time.
- Convenience for Slag Dumping
- For ladles below 15T, the sliding nozzle bottom injection design allows easy slag removal.
- Optional manual rotation mechanism (worm gear reducer) provides user-friendly operation.
- Efficient Gear System
- Features a steel bevel gear and copper worm gear combination for smooth speed reduction.
- Ensures stable rotation and excellent self-locking performance for precise and controlled pouring.
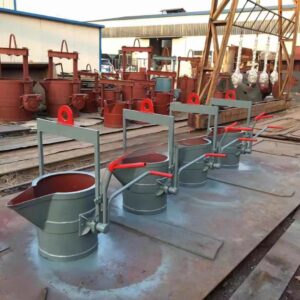
This robust and reliable bottom injection ladle offers enhanced functionality, durability, and safety, making it an essential tool for foundry operations requiring precision and efficiency.
Customizable Foundry Ladle Solutions
The Foundry Ladle is primarily designed for the pouring and handling of molten metal in foundry operations. It can also function as a transfer ladle, ensuring efficient and safe molten metal transport within your facility.
We specialize in custom ladle design and manufacturing tailored to meet your company’s specific technical and operational requirements, ensuring optimal performance and compatibility with your production processes.
Trust us to provide reliable, high-quality ladles that enhance your foundry’s efficiency and safety standards.
Casting Hot Metal Ladle Advantages
The Casting Hot Metal Ladle offers exceptional features designed for efficiency, safety, and durability in foundry operations.
Pouring Equipment for Casting Key Advantages
- Optimized Rotation Center:
- Ensures easy operation and allows for reuse after pouring.
- Double Worm Gear Transmission:
- High-precision design with smooth, flexible operation.
- Provides excellent bidirectional reversibility and secure self-locking.
- Enhanced Safety and Durability:
- Forged suspender offers greater reliability compared to steel plate weldments.
- Thick cladding steel plates and triple-reinforced bottom structure (taper, bottom hoop, and welding) extend service life and protect operators.
- Chain clamp plates on the main body, suspender, gearbox, and handwheel ensure secure locking at any position.
- Self-Aligning Bearings:
- Trunnions and suspenders with self-aligning bearings improve stability and consistency.
- Premium Worm Gear System:
- Copper worm gear and quenched steel worm provide a secure, reliable, and long-lasting drive system.
- Designed to minimize common breakdowns with smooth and flexible handwheel operation.
Maintenance Guidelines
- Refractory Mortar Lining:
- Wall and bottom thickness recommendations:
- 0.5–3 tons: 60–80 mm
- 5 tons: 80–100 mm
- 10 tons: 100–120 mm
- >10 tons: 150 mm
- Wall and bottom thickness recommendations:
- Handwheel Check:
- Ensure the handwheel moves freely without jams.
- Trunnion Bearings:
- Lubricate with molybdenum disulfide grease weekly.
- Wheel Lock Plate:
- Verify the safety and reliability of the lock mechanism.
- Gearbox Maintenance:
- Inspect for oil levels weekly to prevent wear and tear.
- Worm Gear Pair Replacement:
- Replace when clearance increases to ensure safety during pouring.
This hot metal ladle is an indispensable piece of equipment in foundries, combining advanced design, robust construction, and user-friendly operation for optimal performance.