Molten Metal Heating Machine in Investment Casting
Precision at the Core
In investment casting, precise control of molten metal heating machine ensures the integrity and performance of final components. KEWEI’s advanced heating systems—from induction melters to vacuum furnaces—deliver unmatched temperature accuracy (±2°C), minimal oxidation, and energy efficiency for aerospace, medical, and automotive industries.
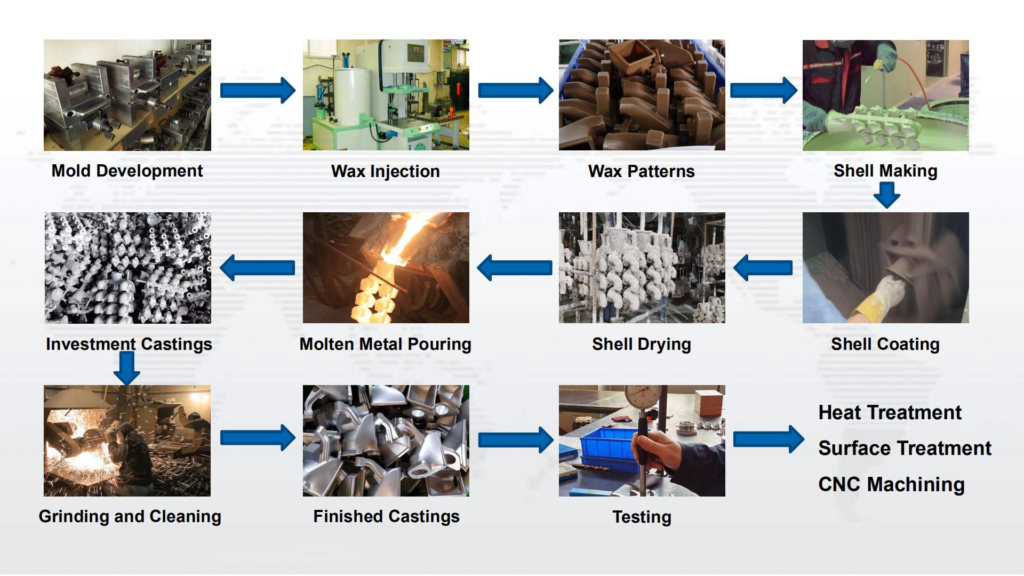
Why Molten Metal Heating Machines Are Vital
- Material Purity: Eliminate impurities and gas porosity in alloys like titanium and stainless steel.
- Temperature Stability: Maintain consistent heat for uniform metal flow.
- Energy Efficiency: Reduce power consumption by 30% with smart heat recovery.
- Versatility: Compatible with reactive metals (e.g., zirconium) and high-volume production.
Why KEWEI? Our molten metal heating machines are trusted by leading investment casting manufacturers for ISO 9001-certified performance.
Key Molten Metal Heating Machines by KEWEI
- Vacuum Induction Melting (VIM) Furnaces
- Function: Melt reactive metals under vacuum (oxygen <5ppm).
- KEWEI Edge: Ideal for aerospace titanium alloys and medical-grade cobalt-chrome.
- Medium-Frequency Induction Heaters
- Function: Rapidly heat aluminum, copper, and stainless steel.
- KEWEI Edge: Frequency-adaptive technology for 95% energy efficiency.
Metal Melting Machine in Investment Casting
- Gas-Fired Tilting Furnaces
- Function: Cost-effective heating for non-reactive alloys (e.g., bronze).
- KEWEI Edge: Low NOx emissions compliant with global environmental standards.
- Resistance Heating Systems
- Function: Pre-heat ceramic molds to prevent thermal shock.
- KEWEI Edge: Multi-zone temperature control (±3°C) for large molds.
Foundry Shell Roaster
Applications of KEWEI’s Heating Machines
- Aerospace: Melt titanium for turbine blades with zero porosity.
- Medical: Ultra-pure platinum alloys for surgical implants.
- Automotive: Aluminum heating for lightweight EV battery housings.
- Energy: High-nickel alloys for corrosion-resistant offshore components.
Case Study: A top investment casting factory reduced energy costs by 40% using KEWEI’s induction heating systems for stainless steel valves.
How to Select the Right Molten Metal Heating Machine
- Material Type: Choose vacuum furnaces for reactive metals or induction heaters for aluminum/copper.
- Production Scale: Match equipment capacity (lab-scale to 10-ton batches).
- Automation: Opt for IoT-enabled systems with real-time monitoring.
- Sustainability: Prioritize energy recovery and emission control features.
Why KEWEI? We provide molten metal heating machines tailored to your needs, backed by 24/7 global technical support.
FAQs About Molten Metal Heating Machines
Q: What’s the difference between induction and resistance heating?
A: Induction uses electromagnetic fields for rapid melting; resistance heats via electric coils for steady temperature control.
Q: Can KEWEI’s machines handle high-purity alloys?
A: Yes! Our VIM furnaces achieve purity levels >99.99% for medical and aerospace applications.
Q: How do I reduce oxidation during heating?
A: Use vacuum or inert gas (argon/nitrogen) environments—standard in KEWEI’s systems.
Upgrade Your Investment Casting Process with KEWEI!
✅ Free Material Test: Verify alloy quality in our advanced lab.
✅ Custom Quote: Get pricing tailored to your production scale.
✅ Fast Installation: Operational in 4–6 weeks with global support.
Ready to upgrade your foundry? Explore our curated selection of advanced metal casting solutions and request a personalized consultation today!