Lost Wax Stainless Steel Casting Equipments
Precision Engineering for Corrosion-Resistant Components
Introduction
Stainless steel’s exceptional corrosion resistance and strength make it a top choice for medical, marine, and food processing applications. At KW Casting, our lost wax stainless steel casting equipments is engineered to overcome the unique challenges of molding this alloy—from high melting points to oxidation risks. This guide explores how our precision systems deliver flawless stainless steel components while adhering to ASTM, DIN, and ISO standards.
Why Stainless Steel Demands Specialized Lost Wax Equipments
Casting stainless steel (e.g., 304, 316, 17-4PH) requires precise thermal control and oxidation prevention. Key challenges include:
- High Melting Temperatures (1,400–1,500°C): Demanding furnace durability.
- Chromium Oxidation Risks: Requires inert gas or vacuum environments.
- Post-Casting Hardness: Needs controlled cooling to avoid stress cracks.
KW Casting’s stainless steel investment casting machines integrate advanced solutions to tackle these issues, reducing scrap rates by up to 40%.
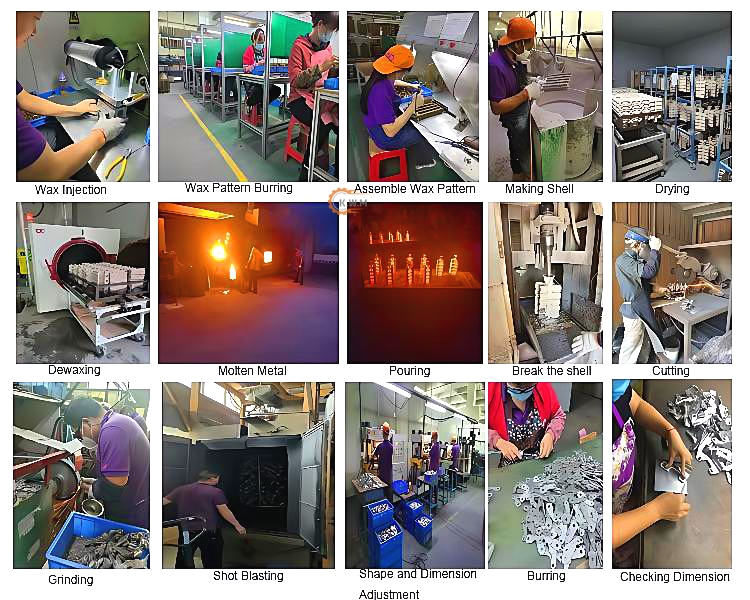
Core Equipment for Stainless Steel Lost Wax Casting
1. High-Temperature Wax Injection Systems
- All-Steel Molds: Withstand aggressive wax injection pressures (15–25 MPa) for complex geometries.
- Oxidation-Resistant Nozzles: Prevent carbon pickup during wax filling.
- Precision Cooling Channels: Ensure uniform wax solidification for minimal distortion.
2. Vacuum Melting & Pouring Systems
- Vacuum Induction Furnaces (VIM):
- Melt stainless steel under <5 ppm oxygen levels to retain chromium content.
- Precise temperature control (±10°C) for grades like 316L or duplex steels.
- Tilt-Pour Mechanisms: Minimize turbulence to prevent slag entrapment in thin-walled parts.
3. Post-Casting Processing Equipment
- Solution Annealing Ovens: Restore corrosion resistance by dissolving carbides at 1,050–1,100°C.
- Electropolishing Stations: Achieve Ra <0.2µm finishes for hygienic (FDA, EHEDG) applications.
- Passivation Tanks: Apply nitric or citric acid treatments to enhance surface oxide layers.
Technological Innovations in Stainless Steel Casting
1. AI-Optimized Thermal Management
- Machine learning adjusts furnace ramp rates and cooling curves based on alloy grade (e.g., martensitic vs. austenitic).
- Reduces energy use by 25% while preventing thermal shock.
2. Hybrid Shell-Building Systems
- Ceramic shells with zirconia inner layers resist metal penetration at high temps.
- Robotic slurry applicators ensure uniform thickness for critical tolerances (±0.1mm).
3. IoT-Enabled Quality Assurance
- Real-time spectroscopy analyzes molten steel composition during pouring.
- Automated X-ray inspection detects porosity or inclusions in castings.
Industrial Investment Casting Factory
Industry Applications of Stainless Steel Lost Wax Casting
- Medical: Surgical instruments, implantable devices (ASTM F138/F139 compliant).
- Food & Beverage: Sanitary valves, pump housings meeting 3-A Sanitary Standards.
- Marine: Corrosion-resistant propeller shafts and marine hardware.
- Energy: High-pressure valve bodies for offshore oil rigs.
How to Select Stainless Steel Lost Wax Equipment
Key factors for optimal stainless steel casting machinery:
- Furnace Atmosphere Control: Vacuum or argon gas systems for oxidation prevention.
- Cooling Rate Adjustability: Water quenching vs. controlled air cooling for desired microstructure.
- Compliance: Equipment meeting NACE MR0175 for sour service environments.
Pro Tip: Choose modular systems like KW Casting’s SteelCast Pro Series to switch between stainless grades (e.g., 304 to 17-4PH) seamlessly.
KW Casting’s Competitive Advantages
As a leader in stainless steel casting equipment manufacturing, we provide:
✅ Grade-Specific Solutions: Tailored setups for 300-series, duplex, and precipitation-hardening steels.
✅ Turnkey Integration: From wax injection to passivation, all under one roof.
✅ Lifetime Technical Support: Remote diagnostics and global spare parts network.
Download Our Stainless Steel Casting Guide
Case Study: Elevating Marine Component Durability
A client producing 316L stainless steel ship fittings faced pitting corrosion in saltwater. KW Casting implemented:
- Vacuum Melting Furnace: Reduced oxygen content to 3 ppm.
- Post-Cast Laser Cladding: Applied a nickel alloy layer on critical surfaces.
Result: Component lifespan extended by 200%, achieving DNV-GL certification.
Conclusion
Investing in specialized lost wax stainless steel casting equipment ensures your components meet the highest corrosion, strength, and hygiene standards. Partner with KW Casting to leverage technology compliant with ASME BPE, ISO 5832, and NORSOK M-650. Contact us for a free alloy analysis and process optimization plan.
Keywords:
- Lost wax stainless steel casting equipment
- Stainless steel investment casting machines
- Precision stainless steel casting tools
- Vacuum melting furnaces for steel
- Corrosion-resistant casting equipment
- Medical-grade stainless steel casting
- Marine component casting systems
Call to Action:
Craft Corrosion-Resistant Components Today!