Investment Casting Tools
Precision Engineering for Flawless Metal Components
Introduction
Investment casting tools are the unsung heroes behind intricate metal components, enabling foundries to achieve tight tolerances and complex geometries. At KW Casting, we engineer casting tool that streamline every stage of the lost-wax process, from pattern creation to final shelling. This article reveals how our tooling solutions empower industries like defense, energy, and robotics to overcome production bottlenecks.
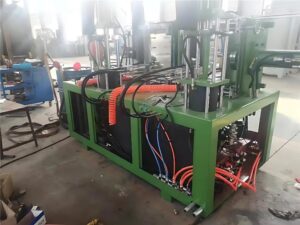
Core Components of Investment Casting Tooling
A robust investment casting machines integrates three critical elements:
- Precision Wax Molds:
- CNC-machined aluminum or steel molds with ±0.02mm accuracy.
- Modular designs for rapid pattern changes (e.g., turbine blades vs. valve bodies).
- Ceramic Shell-Building Tools:
- Automated slurry coating systems with viscosity control.
- Stucco applicators ensuring uniform refractory layers.
- Post-Casting Finishing Tools:
- Vibration-free cutters for gate removal.
- Electrochemical polishing equipment for aerospace-grade surfaces.
Investment Casting Tools
Why Advanced Investment Casting Tools Reduces Defects by 35%
Modern casting machines tackle common failure points:
- Thermal Distortion: Tools with Invar® alloy inserts minimize warping during wax cooling.
- Shell Cracking: AI-monitored drying chambers adjust humidity in real time.
- Dimensional Drift: Laser-guided alignment fixtures maintain consistency across batches.
KW Casting’s patented rapid tooling systems slash lead times by 50% compared to traditional methods.
Industry-Specific Tooling Innovations
Aerospace & Defense
- Conformal Cooling Channels: Tools with 3D-printed cooling paths reduce cycle times for superalloy parts.
- Split-Cavity Molds: Enable undercut geometries for fuel nozzles and turbine vanes.
Medical Implants
- Micro-Tolerance Tools: Achieve Ra 0.4µm surface finishes for titanium orthopedic devices.
- Biocompatible Wax Compatibility: Tools optimized for FDA-approved medical-grade waxes.
How to Select Investment Casting Tools
When sourcing foundry casting tools, prioritize:
- Material Durability: Tool steels like H13 for 100,000+ cycles.
- Automation Readiness: Robotics-ready fixtures for Industry 4.0 integration.
- Supplier Expertise: Look for ISO 9001-certified partners like KW Casting.
Pro Tip: Use FEA (Finite Element Analysis)-validated tools to predict stress points in high-volume production.
KW Casting’s Tooling Solutions: Beyond Standards
As a leader among investment casting tool manufacturers, we offer:
✅ On-Demand Redesign Services: Retrofit legacy tools with IoT sensors for predictive maintenance.
✅ Cost-Per-Part Guarantee: Tools engineered to reduce per-unit costs by 22-30%.
✅ Global Logistics Support: 72-hour emergency tool replacement in 15+ countries.
Conclusion
Superior investment casting tools transform prototyping into scalable production. Partner with KW Casting to access tooling that aligns with AS9100 and NADCAP standards. Contact us for a free defect analysis and tooling ROI calculator.