Investment Casting Surface Finish
The Key to High-Performance Components
The Investment Casting Surface Finish directly impacts performance, aesthetics, and cost. At KEWEI, we combine precision casting processes and advanced finishing technologies to achieve surface roughness as low as Ra 0.4μm, eliminating costly post-processing for industries like aerospace, medical, and automotive.
Factors Influencing Investment Casting Surface Finish
- Ceramic Shell Quality: Smooth ceramic molds reduce surface defects.
- Metal Pouring Technique: Vacuum casting minimizes porosity and inclusions.
- Post-Casting Processes: Shot blasting, grinding, and electropolishing refine surfaces.
- Material Choice: Stainless steel, titanium, and superalloys respond differently to finishing.
Why KEWEI? Our integrated approach ensures precision surface finishes from mold design to final machining.
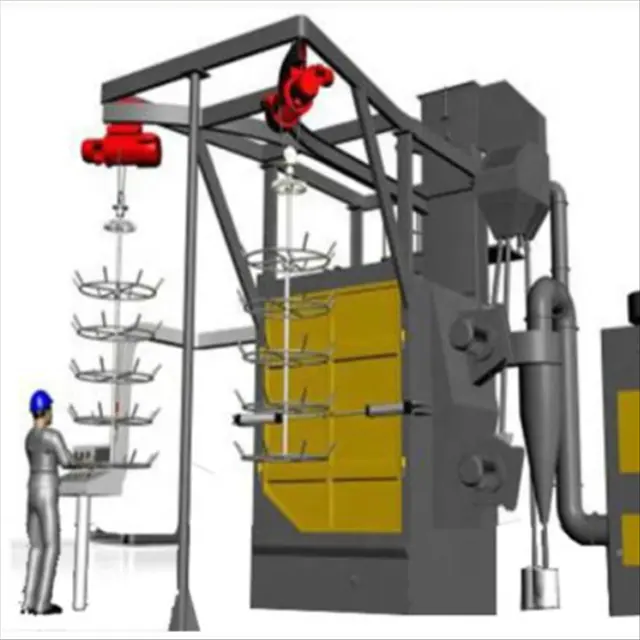
KEWEI’s Surface Finish Solutions for Investment Casting
- Ceramic Shell Optimization
- Technology: Nano-coated ceramic slurries for ultra-smooth molds.
- Result: Surface roughness ≤Ra 1.6μm directly from casting.
- Vacuum Casting Systems
- Function: Eliminate gas porosity and oxide layers.
- KEWEI Edge: Vacuum levels ≤30mbar for aerospace-grade components.
- Post-Casting Finishing Equipment
- Shot Blasting Machines: Remove residual ceramic and micro-burrs.
- CNC Grinding & Polishing: Achieve Ra 0.4μm for medical implants.
- Electropolishing Systems: Create mirror finishes on stainless steel parts.
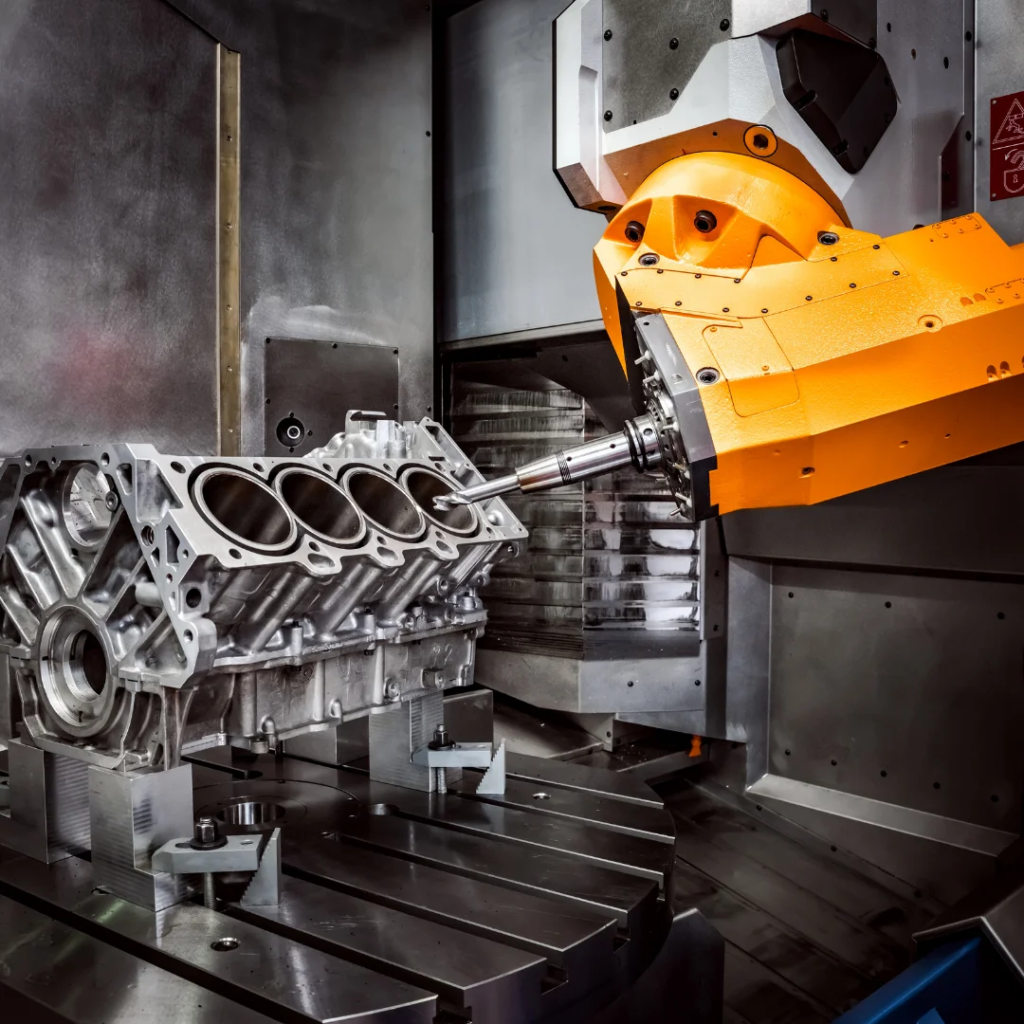
Applications of KEWEI’s Surface Finish Expertise
- Aerospace: Turbine blades with Ra 0.8μm for reduced aerodynamic drag.
- Medical: Electropolished titanium implants (Ra 0.2μm) for biocompatibility.
- Automotive: As-cast aluminum housings with Ra 3.2μm, eliminating machining.
- Luxury Goods: Mirror-finished watch cases and jewelry.
Case Study: A medical device manufacturer reduced post-casting costs by 45% using KEWEI’s integrated vacuum casting and electropolishing systems.
How to Improve Lost wax Casting Surface Finish
- Optimize Ceramic Slurry: Use fine-grained zircon or fused silica.
- Control Pouring Parameters: Temperature, vacuum level, and metal flow rate.
- Select Post-Processing Tools: Match finishing methods (e.g., shot blasting vs. electropolishing) to material and application.
- Leverage Automation: Robotic polishing for consistency in high-volume production.
Why KEWEI? We provide turnkey surface finish solutions, from mold design to final inspection.
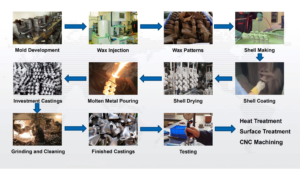
FAQs About Investment Casting
Q: Can as-cast surfaces meet Ra 1.6μm without machining?
A: Yes! KEWEI’s nano-coated ceramic shells achieve this for aluminum and stainless steel.
Q: How does electropolishing improve corrosion resistance?
A: It removes surface impurities and creates a passive oxide layer, ideal for medical and marine applications.
Q: What’s the cost of improving surface finish?
A: KEWEI’s optimized processes reduce post-processing costs by 30–50% through integrated solutions.
Ready to Perfect Your Casting Surface Finish?
✅ Free Surface Analysis: Send a sample for Ra testing and improvement recommendations.
✅ Custom Quote: Get pricing for integrated casting and finishing solutions.
✅ Global Support: Installation and training in 30+ countries.
Ready to upgrade your foundry? Explore our curated selection of advanced metal casting solutions and request a personalized consultation today!