Dewaxing Kettle for Investment Casting
Achieving Smooth, Flawless Finishes
Streamline your investment casting process with our state-of-the-art Dewaxing Kettle. Designed for precision and efficiency, this kettle ensures fast and complete wax removal, preparing your ceramic shells for flawless metal casting. Ideal for foundries of all sizes, our Dewaxing Kettle is built to deliver consistent performance and durability.
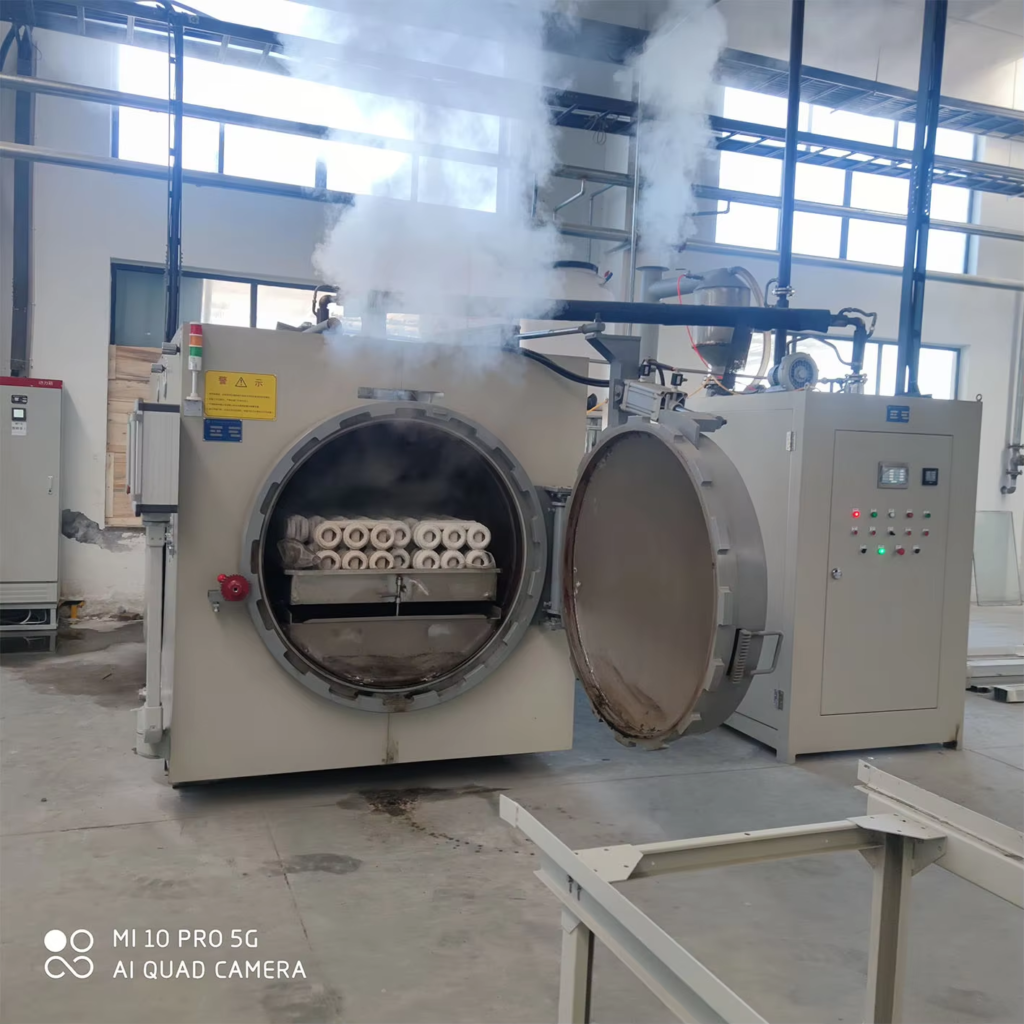
-
Compact and Efficient Design:
This machine integrates an electric heating steam boiler, dewaxing kettle, and gas storage tank into a single unit, significantly reducing the equipment’s footprint. It enhances energy efficiency and improves the working environment. - Double-Layer Pressure Vessel:
Designed as a double-layer pressure vessel, the outer layer operates under high temperature and pressure, maintaining an internal surface temperature above 150°C. This minimizes distilled water formation and ensures low water content in the wax liquid. - Safe and Reliable Operation:
The machine features a manually operated door with a safety chain mechanism. The door cannot be opened unless the exhaust valve is released, ensuring operator safety and preventing accidents. - Automated Control System:
Equipped with automatic water replenishment, temperature control, and pressure regulation, the machine ensures safe and efficient production. Its electric control system provides a seamless and reliable operation. - User-Friendly HMI Interface:
The machine includes a Human-Machine Interface (HMI) for intuitive operation and real-time monitoring. It records each operational step, generates temperature curve charts, and stores multiple control programs for future reference. - Dual Air Inlets for Rapid Pressurization:
With two air inlets, the machine achieves a pressure rise from 0 to 0.8 MPa in under 3 seconds, preventing shell cracking and ensuring consistent performance. - Rotatable Dewaxing Basket:
The dewaxing basket is rotatable, with an adjustable angle of 35° forward and backward. This maximizes wax removal, reduces waste, lowers costs, and minimizes pollution from excessive shell roasting. - Proportional Exhaust Valve:
The machine uses a proportional exhaust valve for staged exhaust, effectively controlling the exhaust speed to prevent shell damage. - Pressure Gauge Cooling System:
A water-cooled front bend on the pressure gauge ensures accurate temperature measurement and extends the gauge’s service life. -
Application and Compliance:
Primarily used for medium-sized shell dewaxing in precision casting, the machine is constructed with 345R pressure vessel-grade materials. It complies with national standards, emphasizing safety, energy efficiency, and environmental protection.
Key Features
- High Efficiency:
- Rapid wax removal with precise temperature control, reducing cycle times and improving throughput.
- Robust Construction:
- Made from high-quality materials to withstand high temperatures and harsh foundry conditions.
- Temperature Control:
- Advanced temperature regulation for optimal wax melting without damaging the ceramic shell.
- User-Friendly Design:
- Easy to operate and maintain, with safety features to protect operators.
- Versatile Application:
- Compatible with various wax types and shell materials, ensuring flexibility for different casting needs.
Dewaxing Kettle
- Compatible with various wax types and shell materials, ensuring flexibility for different casting needs.
Technical Specifications:
Item | Technical parameters |
Design pressure | 1.1Mpa |
Working Pressure | 0.8Mpa |
Operating temperature | 170℃ |
Dewaxing time | ≤3S |
Effective use space | Φ1000×1200/Φ1200×1500 |
Electricity used | 380V 123/147KW |
Weight | 3T |
Water supply pressure | 1~4Mpa |
Water supply capacity | 2.4T/H |
Benefits
- Improved Productivity: Faster wax removal means shorter production cycles and higher output.
- Cost Savings: Reduces energy consumption and minimizes wax waste.
- Enhanced Quality: Ensures clean, defect-free ceramic shells for high-quality castings.
- Durability: Engineered for long-term reliability in demanding environments.
Why Choose Us?
- Expertise: Decades of experience in foundry equipment manufacturing.
- Quality Assurance: Rigorous testing to ensure top performance.
- Customer Support: Dedicated service team for installation, training, and maintenance.
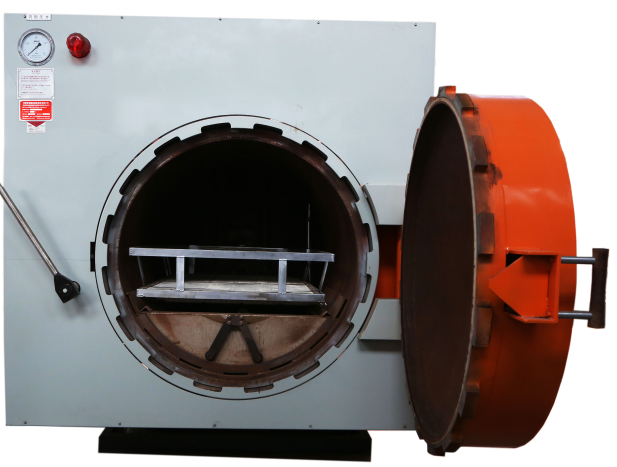
Transform your investment casting process today! Contact us now for a free consultation and discover how our Dewaxing Kettle can enhance your production efficiency.
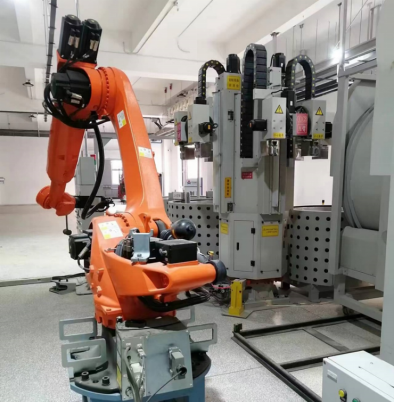
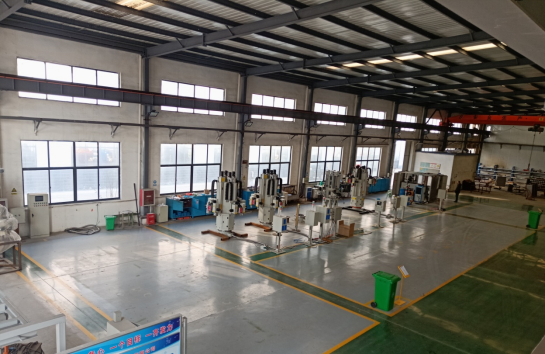
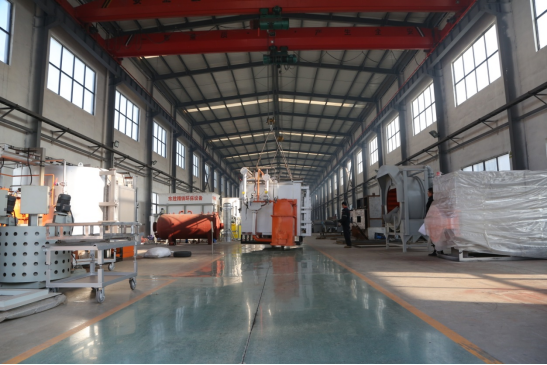
We Also Offer Complete Production Lines in Turnkey Solutions
In addition to the dewaxing kettle, we provide complete turnkey production lines tailored to your specific needs. Our comprehensive solutions ensure seamless integration and optimized production, from start to finish. Turn to Contact us page to talk more with detials.