Investment Casting Ovens
Precision Heating Solutions for Superior Casting Quality
Introduction
Investment casting ovens are indispensable in the lost-wax process, ensuring precise temperature control during critical stages like ceramic shell drying, dewaxing, and metal preheating. At KW Casting, our investment casting ovens combine cutting-edge thermal engineering with smart automation to eliminate defects and accelerate production. This article explores how our ovens optimize casting quality across industries, from aerospace to renewable energy.
Key Roles of Ovens in Investment Casting
A well-designed foundry oven addresses three core process requirements:
- Ceramic Shell Drying:
- Multi-zone humidity control ensures uniform drying of refractory layers.
- Reduces shell cracking risks by maintaining 40–60% RH during curing.
- Dewaxing & Burnout:
- Steam or flash-fire ovens remove wax without residue, critical for complex geometries.
- Rapid ramp rates (up to 15°C/min) minimize energy consumption.
- Preheating Molds:
- Preheats ceramic molds to 800–1,100°C before metal pouring, preventing thermal shock.
KW Casting’s ovens feature IoT-enabled temperature profiling, ensuring ±5°C uniformity across all zones.
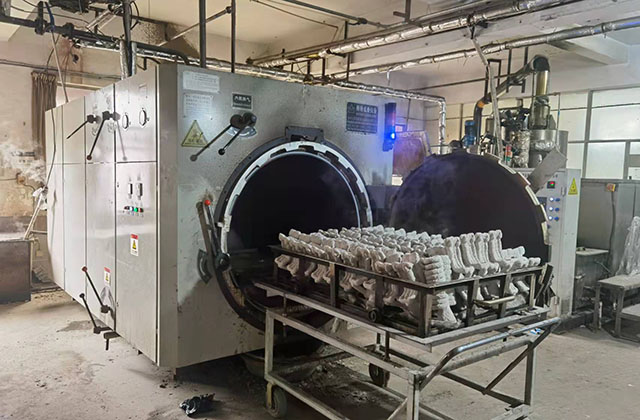
Innovative Features of KW Investment Casting Ovens
1. Adaptive Thermal Management
- AI-Powered Heating Algorithms: Auto-adjust heating curves based on mold size and material.
- Energy Recovery Systems: Capture waste heat to reduce energy costs by 30%.
2. Hybrid Dewaxing Technology
- Combine steam and microwave dewaxing for 50% faster wax removal versus conventional methods.
- Ideal for large-scale automotive or industrial valve castings.
3. Modular Design Flexibility
- Configurable chambers (0.5–15 m³) accommodate prototypes or mass production.
- Retrofittable with robotic loading systems for Industry 4.0 integration.
loast wax casting dewaxing kettle
Industry Applications: Precision Heating for Demanding Sectors
- Aerospace: Precisely preheat molds for nickel-based superalloy turbine blades.
- Medical: Low-oxygen ovens prevent titanium implant oxidation during burnout.
- Automotive: High-throughput ovens for aluminum EV battery housing castings.
- Energy: Dry ceramic shells for wind turbine components with 100% humidity tracking.
How to Select the Right Investment Casting Oven
Choosing an oven requires evaluating:
- Temperature Range: Standard (200–1,200°C) or high-temp (up to 1,600°C) for advanced alloys.
- Heating Method: Electric, gas, or induction-based systems.
- Compliance: Ovens meeting AMS 2750 or NADCAP standards for aerospace workflows.
Pro Tip: Opt for ovens with dual cooling systems (air + water) to prevent warping in thick-shell molds.
KW Casting’s Competitive Advantages
As a leader in industrial casting oven manufacturing, we provide:
✅ 10-Year Refractory Warranty: Guaranteed thermal efficiency and durability.
✅ Turnkey Installation: Includes heat profiling and staff training.
✅ Custom Atmospheres: Nitrogen or argon environments for reactive alloys.
Case Study: Solving Porosity in Castings
A client producing hydraulic valve bodies faced 12% scrap rates due to trapped gas. KW Casting implemented:
- Vacuum-Compatible Oven: Removed air pockets during ceramic shell drying.
- Gradual Preheating Cycle: Reduced thermal stress before aluminum pouring.
Result: Scrap rates dropped to 2%, saving $220K annually.
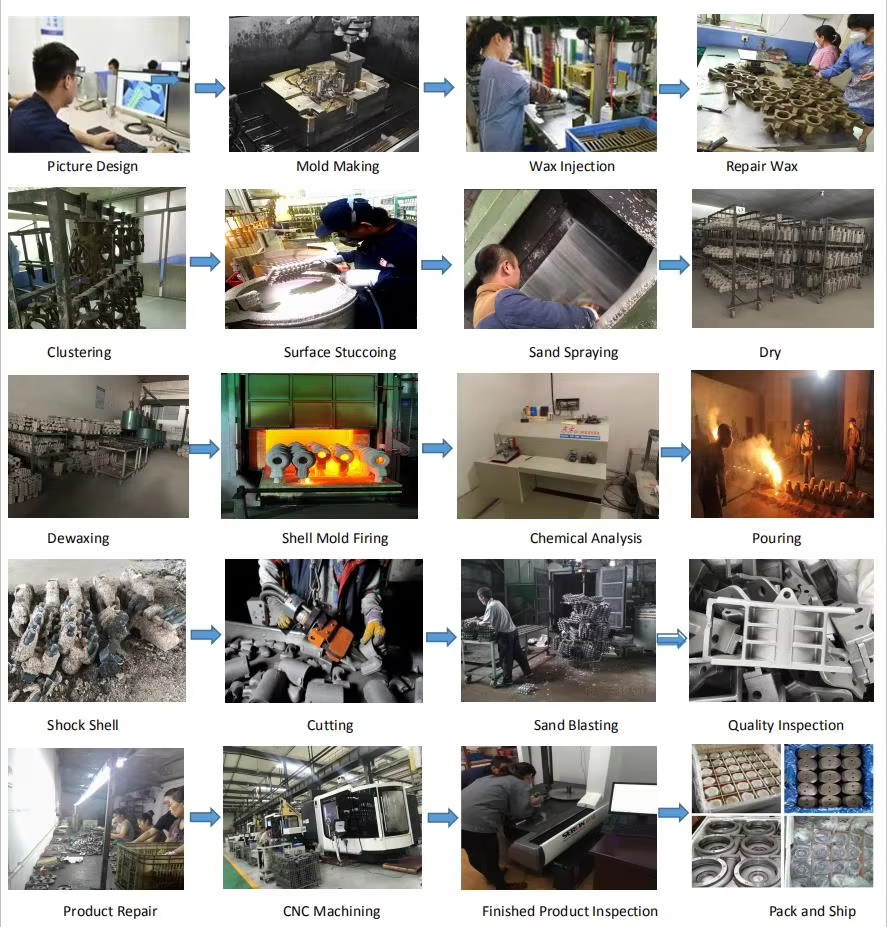
Conclusion
Investing in advanced investment casting ovens ensures consistent quality, reduced waste, and compliance with stringent industry standards. Contact KW Casting to schedule a free thermal efficiency audit and discover how our ovens can cut your energy costs by 25%.
Keywords:
- Investment casting oven
- Ceramic shell drying oven
- Dewaxing oven for foundry
- Preheating oven for casting
- Industrial casting furnace
- High-temperature foundry ovens
- Automated dewaxing systems