Lost Foam EPC Casting Machines
The Complete Guide to Expendable Pattern Casting Technology
1. Lost Foam EPC Casting Machines: Process Overview
What is Lost Foam EPC Casting Machines?
Expendable Pattern Casting (EPC) utilizes foam patterns that vaporize during metal pouring, creating precise, complex aluminum and ferrous castings.
Key Advantages:
✔ No cores required – reduces 30% labor cost
✔ ±0.2mm dimensional accuracy
✔ 75% less machining vs sand casting
Industry Applications:
- Automotive: Engine blocks, cylinder heads
- Pump/Valve: Complex fluid passages
- Machinery: Large, intricate components
Lost Foam EPC Casting Machines
2. Critical Equipment for EPC Casting
Essential Machinery:
Equipment | Function | Key Specs |
---|---|---|
Foam CNC Machines | Pattern machining | ±0.1mm accuracy |
Cluster Assembly Tables | Pattern grouping | Laser alignment |
Vacuum Casting Systems | Metal filling | 0.3-0.6bar vacuum |
Material Innovations:
- STMMA Foam: Low carbon residue for steel
- EPMMA Beads: Superior surface finish
- Nano-Coating: Reduces slag inclusion
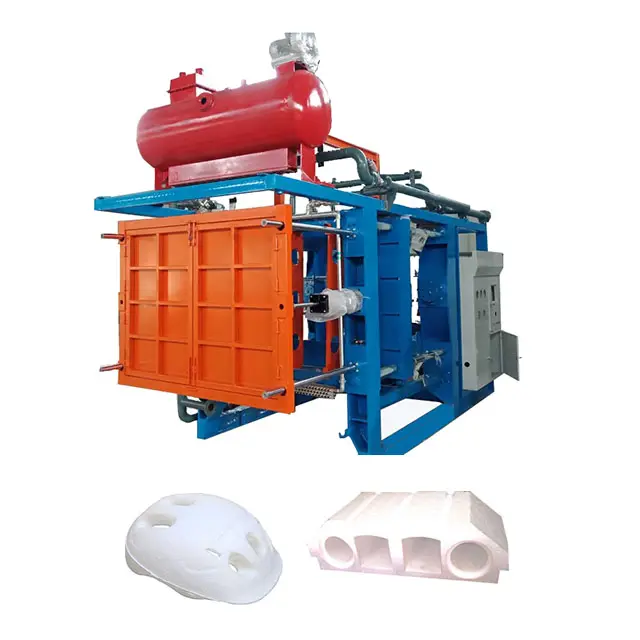
3. Step-by-Step EPC Process
- Pattern Production
- 3D printing or CNC machining EPS/STMMA
- Cluster Assembly
- Hot glue gating system attachment
- Coating Application
- Ceramic slurry dipping (0.5-2mm thickness)
- Sand Compaction
- Vibration tables with 50-100Hz frequency
- Metal Pouring
- Vacuum-assisted filling for thin walls
4. Quality Control Measures
Defect Prevention:
- X-ray Inspection: Detects internal porosity
- Thermal Analysis: Monitors foam decomposition
- 3D Scanning: Verifies dimensional accuracy
Common Solutions:
Issue | Cause | Fix |
---|---|---|
Carbon defects | Incomplete vaporization | Increase pouring temp |
Surface folds | Coating cracks | Adjust slurry viscosity |
5. Cost Comparison: EPC vs Traditional Methods
Automotive Bracket Example:
Factor | Sand Casting | EPC Casting |
---|---|---|
Tooling Cost | $18,000 | $3,500 |
Lead Time | 12 weeks | 3 weeks |
Surface Finish | Ra 6.3μm | Ra 3.2μm |
ROI Case Study:
Foundry achieved 11-month payback through:
- 40% material savings
- 60% reduction in machining
6.Key Procedural Steps in Lost Foam Casting
Source Material for the Pattern:
Selecting the right material for the pattern is crucial in lost foam casting. For aluminum die castings, manufacturers typically use expandable polystyrene (EPS) with pentane as a blowing agent. In contrast, for cast iron and steel parts, a copolymer made of EPS and EPMMA is the preferred choice.
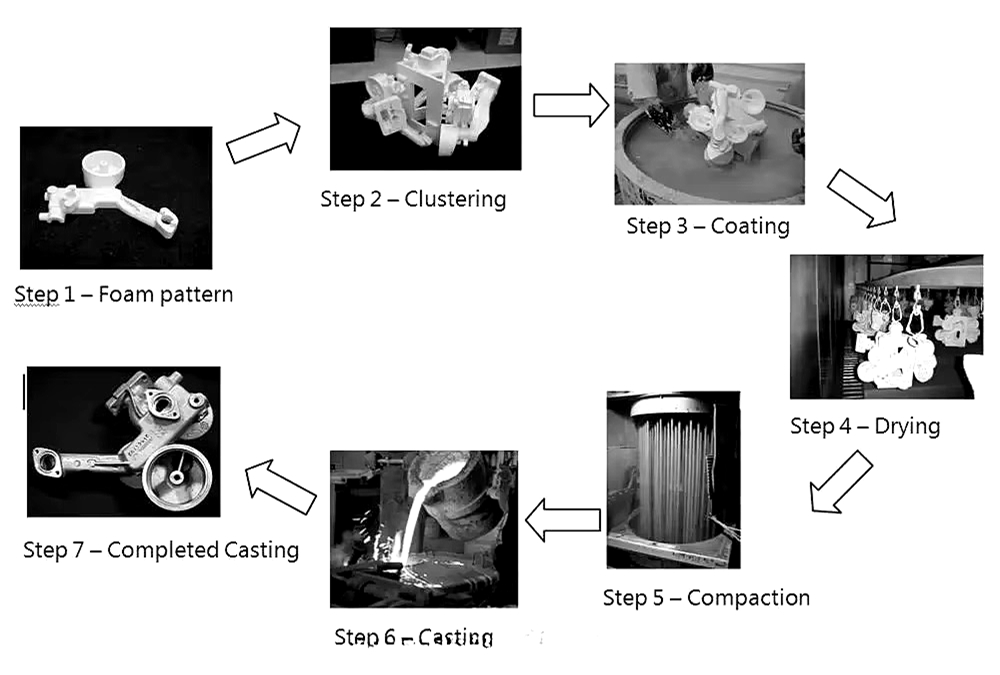
1. Pattern Material Selection
- Aluminum Die Castings:
Use expandable polystyrene (EPS) with pentane as a blowing agent.
Why: EPS is lightweight and decomposes cleanly at aluminum’s lower melting point (~660°C). - Cast Iron/Steel Parts:
Use a copolymer of EPS and EPMMA (expanded polymethyl methacrylate).
Why: The copolymer withstands higher temperatures (iron: ~1,200–1,500°C; steel: ~1,370–1,500°C) and reduces residue.
2. Pre-Expansion
- Process:
EPS beads are pre-expanded in a fluidized bed dryer using pentane (a volatile hydrocarbon).
Purpose: Increases bead size (typically 20–50x) to achieve target density (e.g., 20–30 kg/m³). - Key Control: Temperature and residence time to ensure uniform expansion.
3. Molding
- Tooling: Pre-expanded beads are blown into a metallic permanent mold using compressed air.
- Bonding: Heated (100–120°C) to fuse beads via steam, forming the foam pattern geometry.
- Pattern Design: Complex geometries are split into sections for easier molding, then assembled post-foaming.
4. Pattern Assembly & Gating
- Cluster Assembly:
Multiple foam patterns are mounted onto a gating system (typically EPS) to form a cluster.
Purpose: Enables simultaneous casting of multiple parts in one pour. - Gating Design: Channels must optimize molten metal flow and minimize turbulence.
5. Coating Application
- Refractory Coating:
Clusters are dipped in a water-based ceramic slurry (e.g., alumina, zirconia) to form a 2 mm coating.
Functions:- Prevents sand erosion during pouring.
- Creates a barrier to reduce gas defects from decomposing foam.
- Enhances surface finish.
- Drying: Coated clusters are dried thoroughly to avoid steam explosions during casting.
6. Mold Preparation
- Sand Compaction:
Coated clusters are placed in a flask, surrounded by unbonded quartz sand (grain size 0.1–0.4 mm).- Sand Raining Feeder: Ensures even distribution.
- Vibrating Table: Compacts sand to 90–95% density for stability.
- Sprue Exposure: Only the gating system’s sprue remains exposed for metal pouring.
7. Casting
- Pouring:
Molten metal is poured into the sprue. The heat decomposes the foam (EPS vaporizes; copolymer may leave minor ash).- Metal Flow: Fills the mold cavity precisely, replicating the foam pattern.
- Gas Management: Decomposition gases (pentane, styrene) vent through the permeable coating and sand.
- Critical Factors:
- Pouring temperature and speed to avoid turbulence.
- Foam degradation rate must match metal front advancement.
8. Demolding & Post-Processing
- Solidification: Metal cools in the sand mold (time depends on part size and alloy).
- Shakeout: Sand is removed via vibration, revealing the casting cluster.
- Cutting: Individual castings are separated from the gating system (e.g., sawing, grinding).
9. Sand Recycling
- Reclamation:
Used sand is cleaned (screening, thermal reclamation) to remove debris and residual coating.
Benefits:- Reduces material costs by 90–95%.
- Environmentally sustainable (minimal waste).
10. Why Choose KW Casting’s EPC Solutions
✅ Turnkey Systems: From foam patterns to finished castings
✅ Material R&D: Proprietary coatings for different alloys
✅ Global Installations: 50+ successful EPC lines
Keywords:
- Lost foam EPC casting
- Expendable pattern casting
- EPC casting process
- Foam vaporization casting
- STMMA foam patterns
- Vacuum assisted casting
- Complex aluminum casting
- Foundry pattern equipment