Lost Wax Casting Machinery
Revolutionizing Manufacturing with KEWEI
Lost Wax Casting Machinery plays a vital role in the precision casting process, also known as investment casting. This machinery is designed to produce high-quality castings with intricate details, widely used in industries such as aerospace, automotive, jewelry, and art. By automating and optimizing various stages of the casting process, lost wax casting machinery ensures efficiency, accuracy, and repeatability.
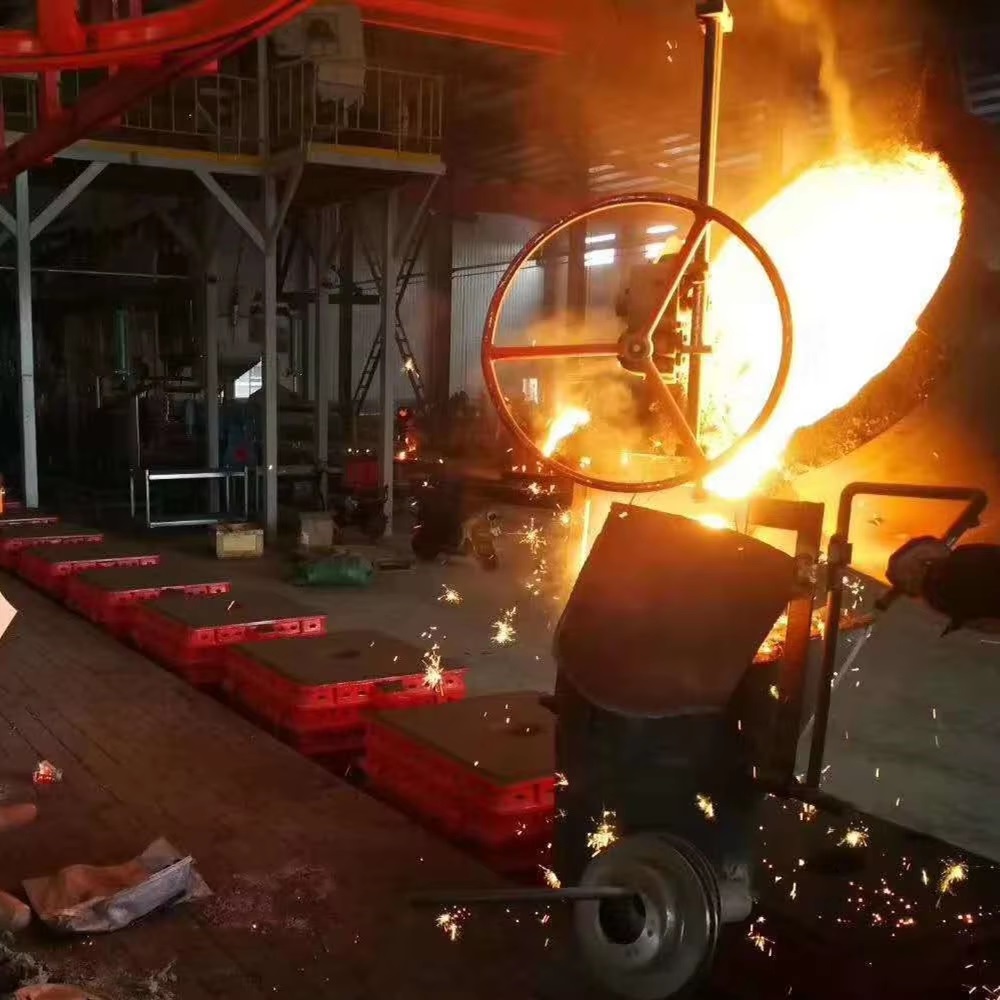
Key Types of Lost Wax Casting
- Wax Injection Machines
- Used to create wax patterns by injecting molten wax into molds.
- Features include adjustable temperature controls, precise pressure regulation, and multi-cavity mold compatibility.
- Dewaxing Autoclaves
- Removes wax patterns from ceramic shells using high-pressure steam.
- Ensures clean removal without damaging the ceramic mold.
- Shell Coating Systems
- Automates the process of applying ceramic slurry and stucco to wax patterns.
- Includes robotic arms, dipping tanks, and fluidized beds for consistent shell thickness.
- Furnaces
- High-temperature furnaces for shell curing and metal melting.
- Includes induction furnaces, resistance furnaces, and gas-fired models.
- Casting Systems
- Pour molten metal into prepared molds with precision.
- Available in manual, semi-automatic, and fully automatic configurations.
- Robotic Arms and Automation Systems
- Used to handle patterns, molds, and castings during production.
- Reduces labor costs and improves consistency.
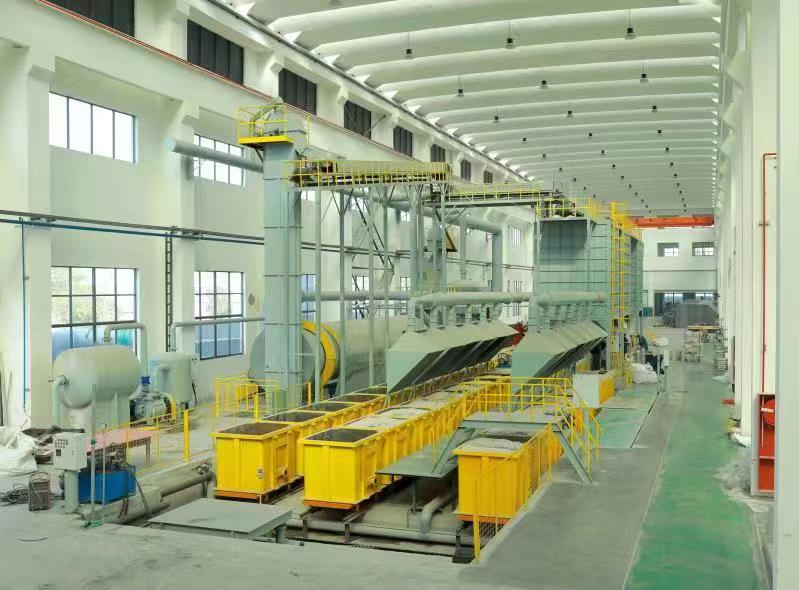
Features and Advantages of Lost Wax Casting Machinery
- Precision and Accuracy
- Ensures intricate details and dimensional accuracy in castings.
- Efficiency
- Speeds up production cycles, reducing time and labor requirements.
- Versatility
- Suitable for various materials, including steel, aluminum, gold, and bronze.
- Durability
- Built with high-quality materials to withstand high temperatures and continuous use.
- Automation
- Incorporates advanced control systems for improved reliability and reduced human intervention.
Applications of Lost Wax Casting Machinery
- Aerospace Industry
- Produces lightweight and high-strength components, such as turbine blades and engine parts.
- Automotive Industry
- Used for manufacturing precision components like gears, valves, and engine parts.
- Art and Sculpture
- Produces detailed sculptures, statues, and decorative items.
- Medical and Dental
- Used for creating implants, surgical tools, and dental prosthetics.
Maintenance Tips for Lost Wax Machinery
- Regular Cleaning
- Remove residue and debris from machinery components to ensure optimal performance.
- Lubrication
- Apply appropriate lubricants to moving parts to reduce wear and tear.
- Inspection
- Check for signs of wear, damage, or misalignment regularly.
- Calibration
- Ensure temperature and pressure controls are accurately calibrated.
- Spare Parts Management
- Keep essential spare parts on hand to minimize downtime during repairs.
Future Trends in Lost Wax Casting
- Digital Integration
- Incorporation of IoT and smart sensors for real-time monitoring and diagnostics.
- Energy Efficiency
- Development of eco-friendly machines with reduced energy consumption.
- 3D Printing Synergy
- Integration with 3D printing technologies to create molds and patterns directly.
- Enhanced Automation
- Use of AI and robotics to further automate the casting process.
- Customization
- Machines designed to cater to specific industry needs and production scales.
Lost wax casting machinery continues to evolve, enabling industries to achieve unparalleled precision and efficiency. By investing in advanced equipment, manufacturers can meet the growing demand for complex and high-quality castings.