Aluminum Investment Casting Machine
Revolutionizing Precision Manufacturing by Kewei
What is Aluminum investment casting ?
Creating aluminum alloy parts directly through casting requires materials with excellent castability. This means good fluidity, minimal shrinkage, and resistance to both hot and cold cracking. It’s also crucial to avoid issues like segregation and gas absorption. Compared to deformed aluminum alloys, cast aluminum alloys generally have higher element content, often near the eutectic composition.
Back in the early 1900s, researchers in Europe and the U.S. explored aluminum alloys for industrial use. While aluminum-nickel alloys were tested, poor casting performance pushed nickel out of the picture. Instead, elements like copper, magnesium, manganese, and silicon took center stage. By the 1920s, silicon-aluminum alloys had become the go-to choice for many industries.
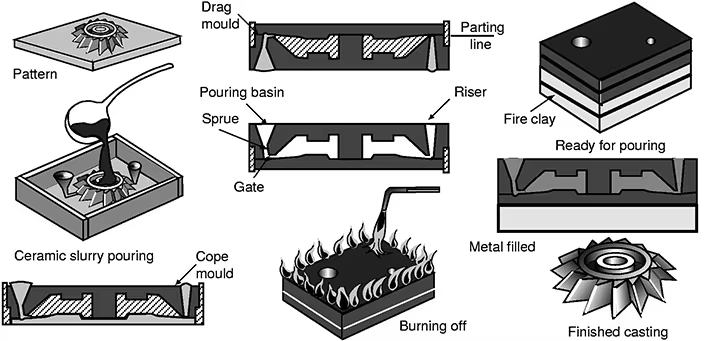
Aluminum investment casting Applications
Cast aluminum alloys are versatile and efficient. They allow for complex shapes, save material, and cut costs without needing heavy machinery. That’s why they’re widely used in industries like aerospace and automotive. Typical applications include aircraft beams, turbine blades, and engine casings. In cars, you’ll find them in cylinder heads, gearboxes, pistons, and more.
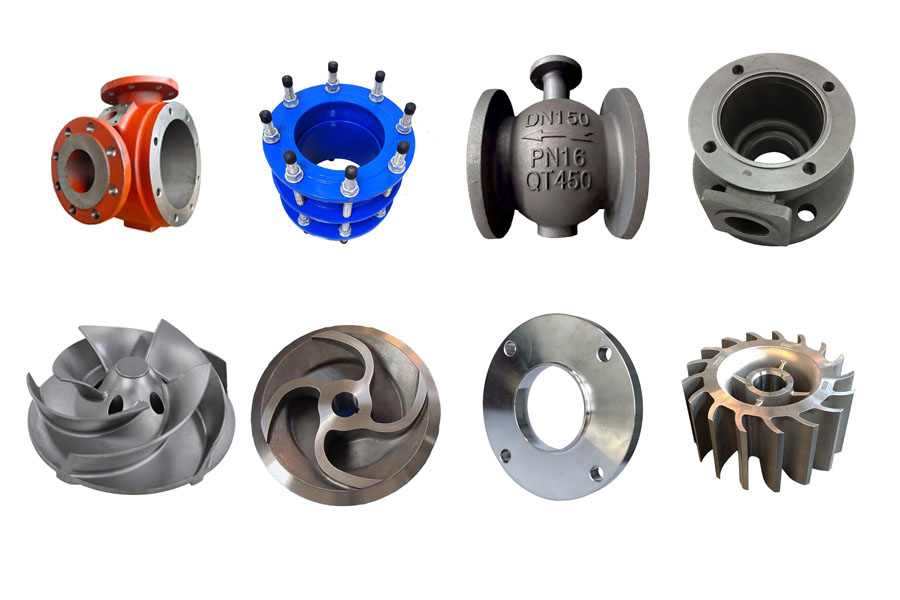
Aluminum Casting Processes
When it comes to aluminum castings, three main methods dominate the field: pressure casting, gravity casting, and extrusion casting. Though they vary in technique, the basic steps remain consistent: smelting the aluminum alloy, making the mold, casting and solidifying, demolding, and finally cleaning. Let’s break down each process.
1. Pressure Casting
Also known as die casting, this method involves using external force—beyond just gravity—to instantly inject molten aluminum into a mold cavity. Within pressure casting, you’ll find subcategories like:
- Vacuum Casting
- Centrifugal Casting
- Low-Pressure Casting
- High-Pressure Casting
And of course, classic die casting completed with specialized machines.
2. Gravity Casting
This process lets gravity do the work, allowing molten aluminum to flow naturally into the mold. It comes in two forms:
- Sand Casting
This method is perfect for single or large-scale production due to its simplicity and affordability. It’s essentially the “bread and butter” of aluminum casting processes. - Metal Mold Casting
Also called hard mold casting, this involves pouring molten aluminum into a durable metal mold made of strong materials like high-grade aluminum alloys. Think of it as the injection molding of aluminum casting—perfect for repeated use.
3. Extrusion Casting
Also known as liquid die forging, this method starts with molten aluminum poured into an open mold. After sealing the mold, high pressure is applied, solidifying the aluminum and shaping it precisely. This process not only ensures uniformity but also produces dense, high-strength castings.
4.Other Techniques
While pressure, gravity, and extrusion casting are industry staples, alternative methods like ceramic casting and gypsum casting are also used for specific needs.
Smooth Surfaces and High Precision
One standout feature of aluminum castings is their incredibly smooth finish. This is thanks to high-precision molds coated with refractory materials that resist heat and wear. The result? Aluminum castings that require minimal post-processing—just polish, and they’re ready to use! This saves time, reduces material waste, and lowers labor costs, making aluminum casting both efficient and economical.
Why choose Kewei’s aluminum investment casting machine ?
1. Powerful Vacuum System
Our machines feature high-efficiency vacuum pumps to create the ideal low-pressure environment. This minimizes oxidation and delivers top-notch material quality.
2. Precision Focused
Whether it’s aerospace parts or delicate jewelry, our machine ensures every detail is perfect—down to the tiniest measurement.
3. Energy-Saving Design
Our systems are built to be eco-friendly, using less energy while maintaining peak performance.
4. Easy-to-Use Interface
Operating our machine is a breeze. With simple controls and an intuitive interface, training your team has never been easier.
5. Built to Last
Made with durable, high-quality materials, our machines can handle the toughest foundry conditions without breaking a sweat.
Kewei Projects:
One of our automotive clients used Kewei’s aluminum investment casting machine e to make ultra-light engine components, boosting fuel efficiency and cutting emissions. Another client, a valve and pump maker, crafted stunning, intricate designs with flawless precision, thanks to our technology.
Upgrade Your Casting Equipments
Looking for a way to take your casting operations to the next level? With Kewei’s aluminum investment casting machine, you’ll get unmatched precision, efficiency, and quality. Whether you’re in aerospace, jewelry, or any other industry, our equipment is built to help your business succeed.
Get in touch today and see how Kewei can revolutionize your production!