Investment Casting Machining
Revolutionizing Precision Manufacturing by Kewei
Investment casting machining, also known as lost wax casting, is a precision manufacturing process that involves several steps: wax injection, wax trimming, tree assembly, slurry coating, wax removal, metal pouring, and post-processing. In this method, a wax model of the desired part is first created. The wax model is then coated with a ceramic slurry to form a mold, which is subsequently dried. Once dried, the mold is heated to melt and remove the wax, leaving a hollow cavity. This ceramic mold is further fired to increase its strength, preparing it for casting.
During the mold-making stage, a pouring gate is incorporated to facilitate the introduction of molten metal. The molten metal is poured into the ceramic mold through this gate, and once the metal cools and solidifies, the mold is removed to reveal the final cast component. This process enables the production of complex and highly accurate parts with excellent surface finishes.
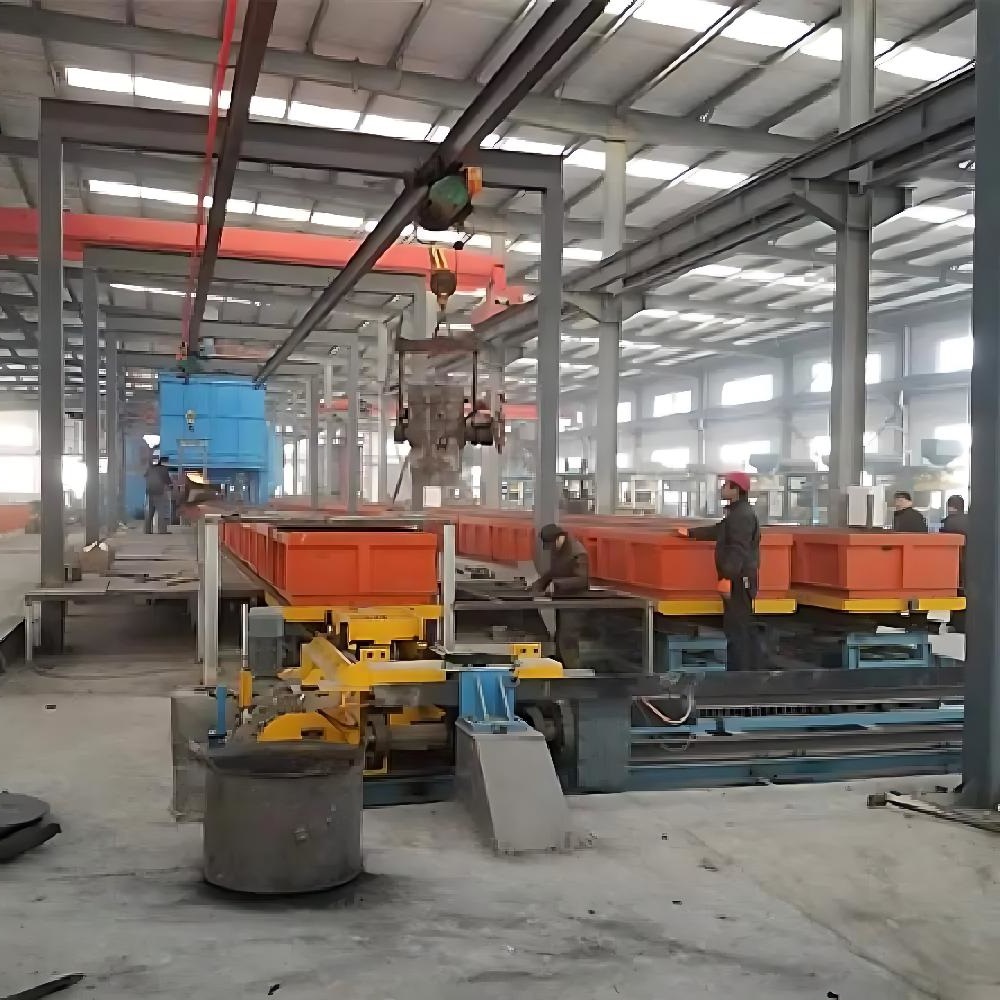
Introduction to Investment Casting Machining
Investment casting, often referred to as “lost wax casting” when wax is used as the pattern material, is a precision casting method. It involves creating a pattern from a fusible material, coating it with multiple layers of refractory material to form a robust shell, and then melting and removing the pattern to produce a mold without parting surfaces. The mold is then subjected to high-temperature firing, after which molten metal is poured into the cavity to produce the casting. This process is especially effective for manufacturing components with intricate designs and tight tolerances.
The term “lost wax casting” is commonly used because wax is the predominant material for creating patterns. The investment casting process accommodates a wide variety of alloys, including carbon steel, alloy steel, stainless steel, heat-resistant alloys, precision alloys, permanent magnet alloys, bearing alloys, copper alloys, aluminum alloys, titanium alloys, and ductile iron.
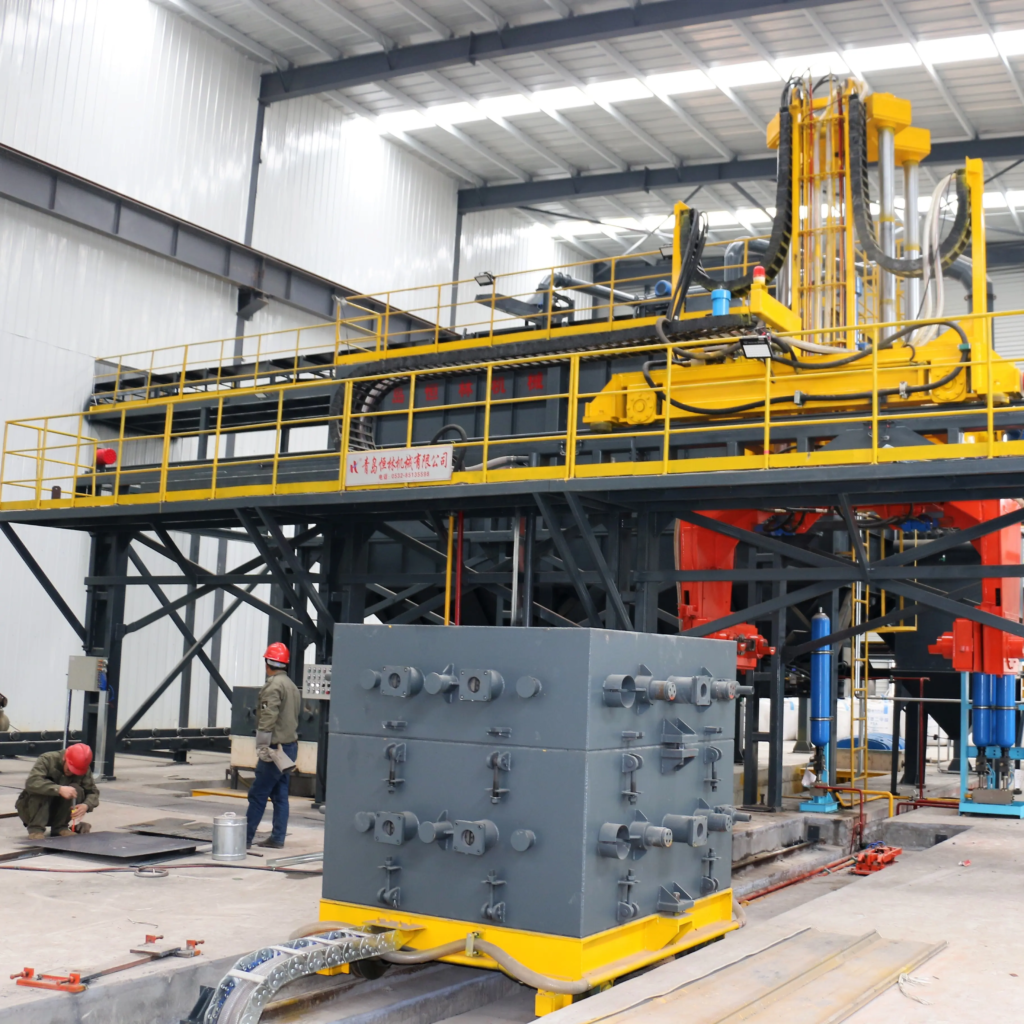
Characteristics of Investment Casting Machining
- Complex Geometries:
Investment castings can achieve highly intricate shapes. For example, the process enables the casting of holes with diameters as small as 0.5 mm and wall thicknesses as thin as 0.3 mm. Moreover, by redesigning parts to integrate multiple components into a single casting, investment casting can save on material costs, machining time, and improve structural efficiency. - Weight Range:
Typical investment castings weigh between a few grams to approximately 25 kilograms. While heavier castings can be produced, they are less commonly made due to the increased complexity and difficulty of the process. - Precision and Surface Quality:
Investment castings offer superior dimensional accuracy, typically achieving tolerances of CT4–6 compared to CT10–13 for sand casting or CT5–7 for die casting. The high surface finish of investment molds and the use of specialized refractory coatings ensure that the surface roughness of castings is excellent, often ranging between Ra 1.6–3.2 μm. - Applications for High-Performance Components:
The process is particularly suited for producing small, intricate components that require high precision and are challenging to manufacture using other methods, such as turbine engine blades. Investment casting is especially beneficial for casting complex high-temperature alloy components, enabling mass production with consistent quality and eliminating residual machining stresses.
Advantages of Investment Casting Machine
- High Dimensional Accuracy:
Investment casting achieves exceptional dimensional accuracy, reducing or even eliminating the need for secondary machining. Only minimal allowances for grinding or polishing may be required, particularly for parts with high precision requirements. - Material Efficiency:
The ability to produce near-net-shape castings minimizes material waste, saving significant amounts of metal raw materials and reducing the reliance on machining processes and equipment. - Superior Surface Finish:
The use of high-quality molds and refractory coatings results in a finer surface finish compared to other casting methods, reducing the need for additional surface treatments. - Capability to Cast Complex Shapes:
Investment casting excels in producing components with intricate designs, such as the aerodynamic contours and internal cooling channels of jet engine blades. These features are challenging or impossible to achieve through conventional machining, making investment casting a critical process for advanced aerospace, energy, and industrial applications.
Investment casting is an advanced manufacturing process that offers unparalleled precision, surface finish, and the ability to produce complex components. While it is more resource-intensive and costly than other casting methods, its advantages make it the preferred choice for high-precision and high-performance applications.
Investment Casting Chinese Domestic Advantages
Information technology is pivotal in developing various industries, particularly in advancing the die-casting mold sector. Leveraging information resources to facilitate timely data processing, seamless communication, and efficient operations is essential for driving innovation and growth in this field.
From the perspective of national macroeconomic policies, industry trends, and both international and domestic market capacities, there is significant demand for large-scale, high-precision, and complex investment casting and die-casting molds. The global market, including the domestic sector, offers substantial opportunities. For instance, the automotive giant Chrysler in the United States has expressed interest in mold design and manufacturing from China, with potential orders reaching a value of 300 million yuan. Companies with robust technical and production capabilities have a strong chance of securing such high-value contracts.
China’s investment casting molds are known for their superior quality, crafted from high-grade materials with excellent workmanship, high dimensional accuracy, and compliance with international standards. These molds have achieved global recognition for their long service life and exceptional casting quality. Furthermore, they maintain a clear competitive edge due to their cost-effectiveness, offering high value at a lower price point.
Investment Casting International Market
China’s investment casting molds are increasingly sought after in key international markets, including Europe, North America, Japan, and South Korea. For some Chinese enterprises, exports now account for over 30% of their total output value, reflecting the growing demand for these products abroad. The decision to invest in large-scale precision mold projects is supported by both theoretical market analysis and practical success, ensuring a calculated approach that yields substantial returns.
For example, Chinese die-casting molds for automobile oil pans exported to Europe have gained widespread acclaim from foreign clients. These molds are highly regarded for their competitive pricing, advanced design, and superior production quality. Repeat orders from international customers demonstrate the strong reputation and growing trust in Chinese-made molds.
The rapid development of China’s investment casting mold industry in overseas markets is evident, and its upward trajectory is expected to continue. With continuous improvements in quality, innovation, and competitiveness, the industry is poised to achieve sustained growth and expand its global presence.